Eliminating Greensand Variation at the Molding Location
A common problem in the foundry industry is proper greensand preparation. Even when the sand is prepared correctly, how is the recipe accuracy determined? How are the results recorded for repeatability purposes? How are changes implemented at the muller? Many foundries monitor their sand by how the molding is performing. Proactive preparation of the greensand, accurately and consistently, will eliminate greensand variation at the molding location.
Removing unwanted variations from the greensand properties is key in producing consistent castings and running a successful foundry. There are many factors that contribute to variations in the way the greensand is prepared and delivered within the foundry. Foundries tend to have different equipment manufacturers and different types of molding processes, that all lend to preparing the greensand with various recipes. The key is defining what type of sand works best for your individual molding equipment.
Many foundries will batch mull their sand for each molding line; which is delivered and stored in the small sand hopper at the machine. This process is a simple solution for individual sand properties at each molding location. If you do not have the capability to batch mull your greensand, then the sand preparation will need to be prepared in a manner that will provide best properties for all equipment. Due to the narrow window of variation of the sand parameters, close monitoring of the sand will be required
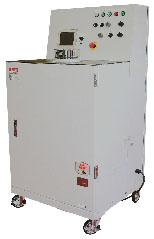
DST-II Sand Tester
In determining of what greensand recipe is right for a foundry, you need to establish what type of sand is to be used and how much clay content is needed. On a daily basis, greensand preparation has five key items that need to be monitored closely for proper molding. These consist of the sand temperature, compactability, moisture content, green compressive strength and permeability.
It is understood that the measurement can be taken at the muller but to get an accurate reading of the five key components, it would best to take a reading at the point that the greensand is used. The Sinto DST-II series provides this solution. This unit allows the user to take readings of the sand make up at any point in the system; this is largely because the DST-II is a portable greensand testing unit. Unlike the fixed sand testing systems that are located in one place, the DST-II can be utilized anywhere. For example, if the sand you are preparing is located on the other end of the foundry, the DST can monitor the sand at the use point such as a jolt squeeze line or molding machine.
Sinto has provided the use of DST-II unit in smaller foundries that do not have in house established testing procedures. In using the DST-II, foundries can process real-time data for the sand they are using within ninety seconds for results.
Sinto has had success in utilizing this testing unit when customers purchase new automated molding lines. Sinto will accurately analyze the sand, removing any variable from the start up procedure when launching new projects. With accurate data, Sinto has been able to launch new machinery in a more timely manner.
DST-II In-Line Digital Sand Testing Unit Features:
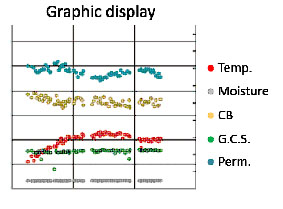
Typical Sand Parameters
- Self-Calibration function
- Repeatable accurate readings
- Can be interfaced with the muller controls to adjust for variability between muller and molding machine
- A load cell is used to is used to conform test sample height which eliminates variance introduced by manually sampling, resulting in highly accurate results
- Measurement data can be exported via USB allowing for easy data transfer for your quality database.
Accurate greensand testing provides foundries with immediate ROI for a small investment. The DST-II is a solution that can be implemented into a foundry at a reasonable cost. The return on investment for DST-II can be calculated by the signification reduction in scrap due to sand defects. Thus eliminating the need to scrap molds due to sand inefficiency.
Want to know more about Sinto’s DST-II Sand Tester?