Foundries of all sizes deserve access to Industry 4.0 tools that are practical, powerful and proven. SINTO SMART FOUNDRY® was built with your unique needs in mind. Whether you’re a small jobbing shop or a multi-facility operation, SSF is fast to install, easy to use and designed to scale with your needs.
Most foundries in North America are small to mid-sized businesses, and SSF meets you where you are — offering enterprise-grade visibility and performance without enterprise-level complexity.
Installation Highlights
- No database setup required
- No need for in-house data scientists or IT teams
- No production downtime during install
- No alterations to existing PLC code
- Out-of-the-box dashboards and alerts
- No hidden maintenance or support costs
- 3-week go-live timeline at the machine level
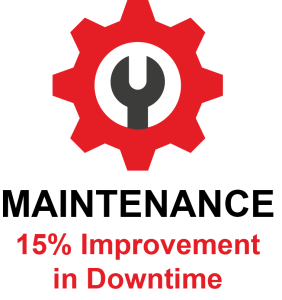
Tired of unplanned downtime and rising repair costs? SSF shifts your team from reactive firefighting to proactive maintenance. With real-time data and expert guidance, you can catch issues before they become costly breakdowns. Many foundries report a 50% decrease in unplanned downtime with Sinto Smart Foundry.
Key Pain Points We Solve
- Unplanned Downtime: Identify failing machines early and prevent production stoppages.
- Spare Part Overuse: Track component health precisely and avoid unnecessary replacements.
- Training Challenges: Equip new maintenance techs with data-driven insights for faster onboarding.
How We Do It
- Real–Time Analytics (BEET): You get instant insights and trending data to identify potential issues before they arise.
- Remote Monitoring Center (RMC): Tap into Sinto’s foundry experts who watch your data, provide proactive recommendations and simply parts ordering.
- Remote Monitoring Sensors (RMS): Install vibration and condition sensors that trigger automated alerts the moment anomalies appear.

Losing revenue to mold defects, inconsistent sand or poor pouring practices? Quality directly impacts your bottom line. SSF gives you real-time visibility across sand, molding and melt departments – reducing scrap and strengthening your continuous improvement initiatives. Many foundries have tracked a 10% to 50% jump in quality with SSF.
Key Pain Points We Solve
- Mold Quality Issues: Spot defects and correct machine setups before the next cast.
- Sand Quality Fluctuations: Monitor sand properties to maintain consistent performance.
- Pouring Irregularities: Reduce scrap by keeping close tabs on melt and pouring parameters.
How We Do It
- Real–Time Analytics (BEET): Gain complete traceability across your processes, so you can pinpoint the root cause of defects and adjust in real time for consistent results.
Remote Monitoring Center (RMC): Tap into Sinto’s foundry experts who provide best practices, troubleshoot pouring and sand issues and help you optimize setups – minimizing scrap and boosting yields.
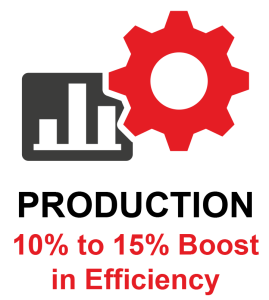
Struggling to track OEE or meet mold-per-hour targets? With SSF, you gain real-time insights to streamline every shift – reducing idle time, optimizing throughput and keeping production on track. Many foundries see a 10% to 15% boost in efficiency after implementing SSF.
Key Pain Points We Solve
- OEE Visibility Gaps: Understand which shifts and machines are falling behind and why.
- Shift Offload Guesswork: Track actual performance and balance workloads in real time.
- Mold-Per-Hour Targets: Pinpoint cycle-time bottlenecks so you can optimize throughput.
How We Do It
- Real–Time Analytics (BEET): Centralizes key metrics like OEE targets, cycle times, operator efficiency and shift data in one place, letting you identify and fix gaps immediately.
- Remote Monitoring Center (RMC): Connects you to foundry experts who assist with operator and maintenance training, ensuring your team sustains optimal uptime.
- Operation Monitor (OpM): Provides high-level dashboards, uptime tracking and even legacy equipment monitoring, so you can spot issues early and keep production running smoothly.
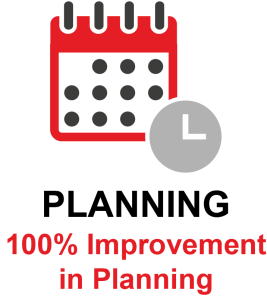
Struggling to decide whether to add or remove a shift? With SSF, you gain real-time insights into actual cycle times, hidden capacity and scheduling requirements so you can plan with confidence. Many foundries see immediate improvements in strategic planning as soon as SSF is deployed.
Key Pain Points We Solve
- Unreliable Scheduling Data: Eliminate guesswork with accurate, up-to-the-minute cycle times.
- Limited Visibility into Capacity: Reveal hidden production potential so you can optimize shifts.
- Workforce Challenges: Offload data monitoring to Sinto’s remote experts, freeing your staff for higher-level tasks.
How We Do It
- Real–Time Analytics (BEET): Provides scheduling tools, production monitors and management reports, letting you plan shifts and outputs based on true performance data.
- Operation Monitor (OpM): Delivers production tracking, spare parts lists and digital manuals so you can streamline planning across both new and legacy equipment.