Farrar Adds BARINDER® & Reduces Grinding Time
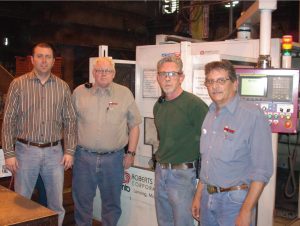
From left to right: Todd Farrar – Vice President, Richard Hicks – Foundry Manager, Rick Wilcox – Barinder Programmer, Lynn Zehr – Pattern Shop Supervisor
In the beginning, there was hand grinding. Parts were non-uniform, progress was slow and injuries weren’t uncommon. After robots came on the scene, parts started to become more uniform, but mistakes could be easily duplicated. They were prone to breakdowns, and although parts could be finished relatively faster, the machines still required a one-to-one ratio to human operators.
Then came the BARINDER® grinders.
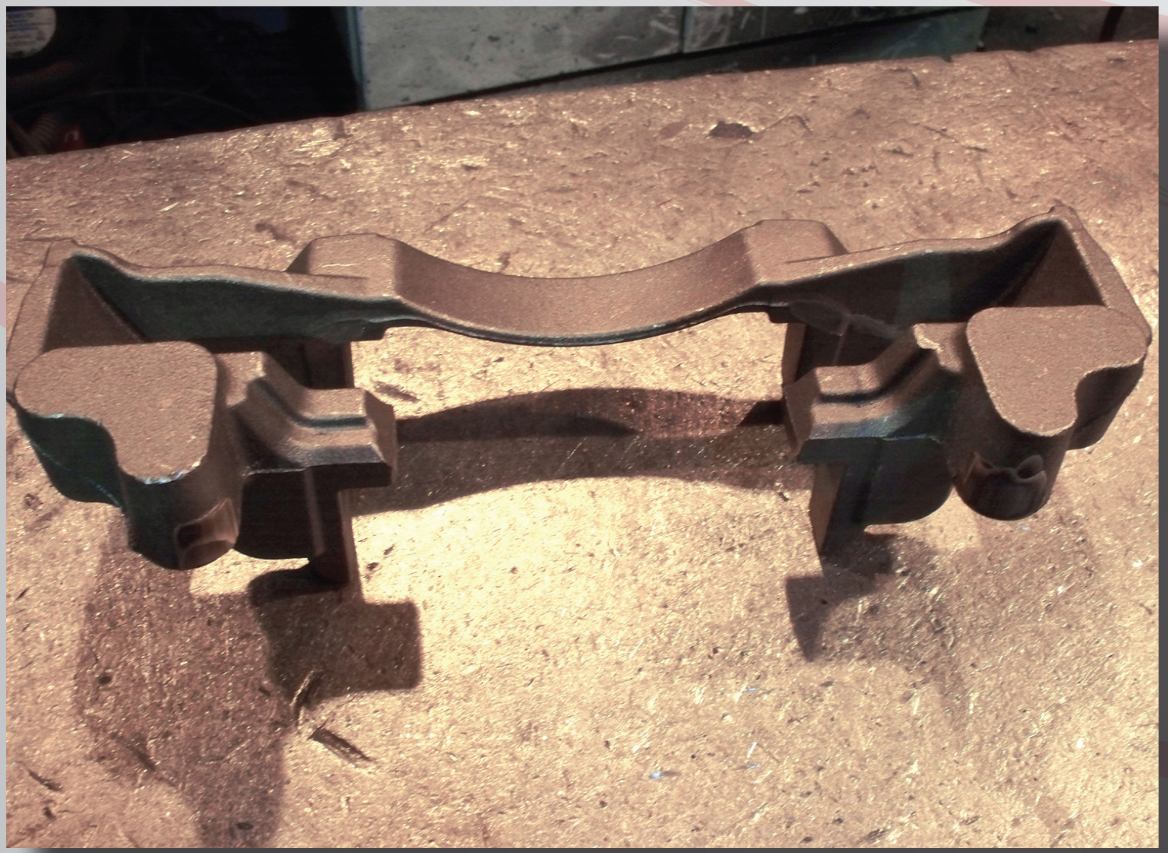
Casting ground on the Barinder
“The Barinders have been an absolute dream,” says Mike Coons, Maintenance Supervisor at Farrar Corporation in Norwich, Kansas. “Since we installed the BARINDER®, we haven’t had any problems that weren’t operator-induced. I’d say it works as well as it was advertised, but that doesn’t even do it justice. It works far better than advertised, and we couldn’t be happier with it.”
Farrar Corporation purchased two BARINDER® grinders in June 2008, both of which were up and operational within 24 hours. The company had been using a competitor’s machine and snag grinders, which at 30 feet long and 20 hp make them both about as big and slow as a brontosaurus when compared to the BARINDER®; and about to become equally as extinct.
“We used to have significant downtime because the competitors auto grinding machines just weren’t built to accommodate the output we expected of them.” says Farrar Corp. president Joe Farrar. “But since the installation of the BARINDER® grinder we’ve had zero downtime. And we work these machines—hard.”
Farrar says that he had become aware of another company that used Barinders and visited them to observe their operation. He sent teams to other foundries to observe other grinders, but the BARINDER® was the one that Farrar says he feels best fit their needs. Farrar’s Foundry Operations Manager Richards Hicks was part of the team that did this field research.
“The BARINDER® is a machine that was designed by foundry men to be used by foundry men,” says Hicks. “We knew that much going into it. It also really helps that the BARINDER® was being marketed by Roberts Sinto. If they put their name on something, we knew it must be good.”
Hicks says that the robot and hand grinding of the past was inefficient and undependable, forcing them to seek out more cost-effective solutions. Human error and slow speed plagued hand grinding, and robot-ground parts often suffered from excessive flash. The Barinder’s flexible part handling features also provide easy and fast part changeover— part holding fixtures can be easily changed with simple hand tools in a matter of minutes.
“Not only has the BARINDER® dramatically increased productivity,” says Joe Farrar, “but the parts it produces are more consistent and the machine is more reliable.”
Barinder’s innovative robotic part handling and unique grinding wheels reliably automate the removal of gates, burrs and parting line fins on gray and ductile iron castings. Most castings can be quickly cleaned in a single set-up, traversing the same path that would be covered in a manual operation. This proven technology enhances the productivity, safety repeatability and environmental integrity of the casting cleaning process. Barinder’s fast robotic cleaning action is further enhanced by an optional second, smaller grinding wheel, making it also possible to clean internal surfaces in areas that would be difficult to reach manually.
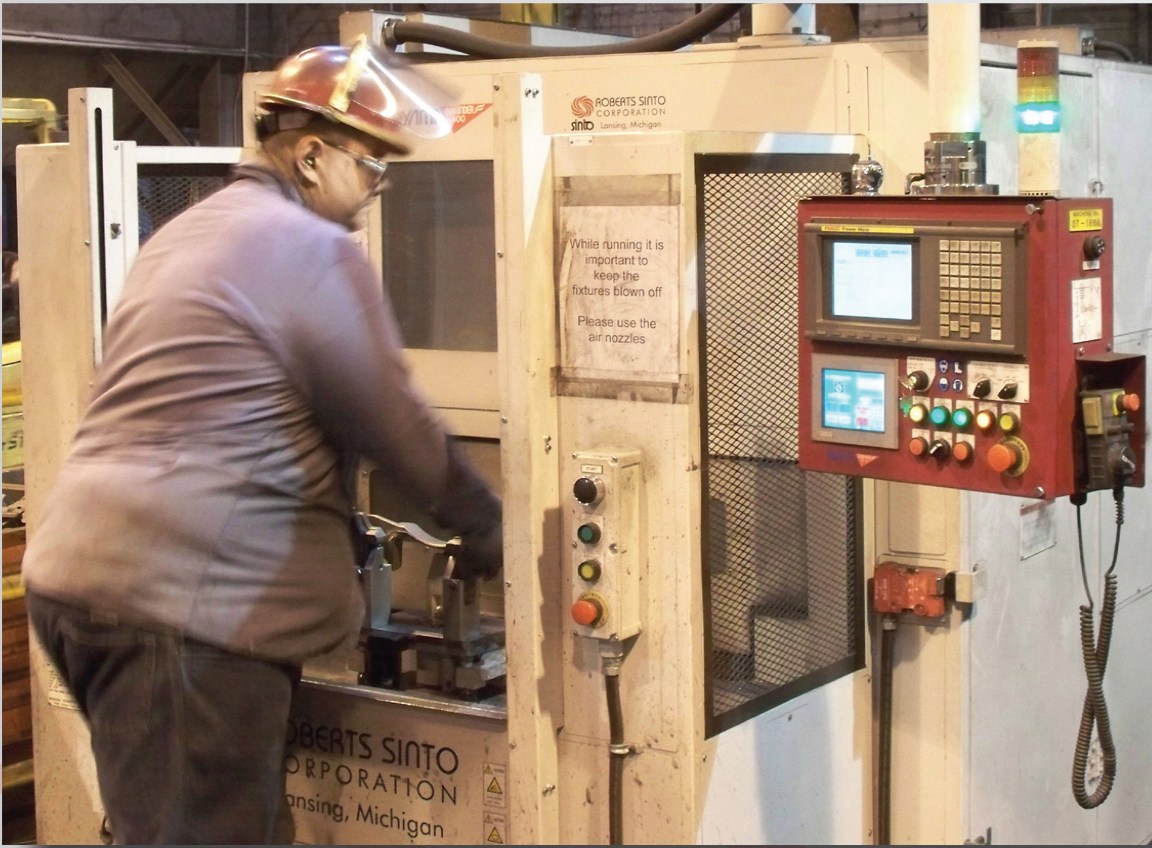
Operator unloads casting from Barinder
“We have been able to program parts on these machines we originally thought weren’t possible” says Rick Wilcox, Foundry Program Specialist. “Programming parts on the Barinder’s is easy and the expected learning curve for teaching employees how to program parts is much shorter than we had anticipated. We are able to move parts from evaluation, fixture and programming stages, to grinding in a very short time.”
“I’ve been in the foundry business for 13 years, and I’ve never experienced any machine like this,” says Coons. “It started lowering manpower in the grinding room from the get-go.”
One person can operate several machines, so now Farrar is able to accomplish the work of three people with only one person. The Barinder is easy to learn and easy to operate, designed to quickly allow the operator to teach-program the machine and to automatically perform tasks that would otherwise be done manually. Not only is the work faster and more energy efficient, but it’s safer as well. All work performed by the Barinder offers quiet operation in an enclosed and isolated environment. The protection offered by the machine enclosure assures the machine operator is not exposed to potentially dangerous rotating wheels, grinding dust or noise.
“In the six months that we’ve had the BARINDER®, we’ve reduced grind time by 50 percent,” says Hicks. “This has improved our bottom line like nothing else before it.”
This streamlining of work means that the BARINDER® produces significant savings in labor costs. Its speed, flexibility and automation capabilities make it an invaluable addition that will dramatically improve grinding efficiency and quality. This makes the machines exponentially more profitable. Any foundry can easily justify the purchase of a Barinder—in fact, after purchasing their initial unit, most foundries have quickly purchased several additional Barinders to handle all grinding requirements.
“This is not a custom machine, which gives us reassurance that there are no bugs to work out,” says Coons. “And we’ve always had a wonderful relationship with Roberts Sinto, especially with their parts department and tech support.”
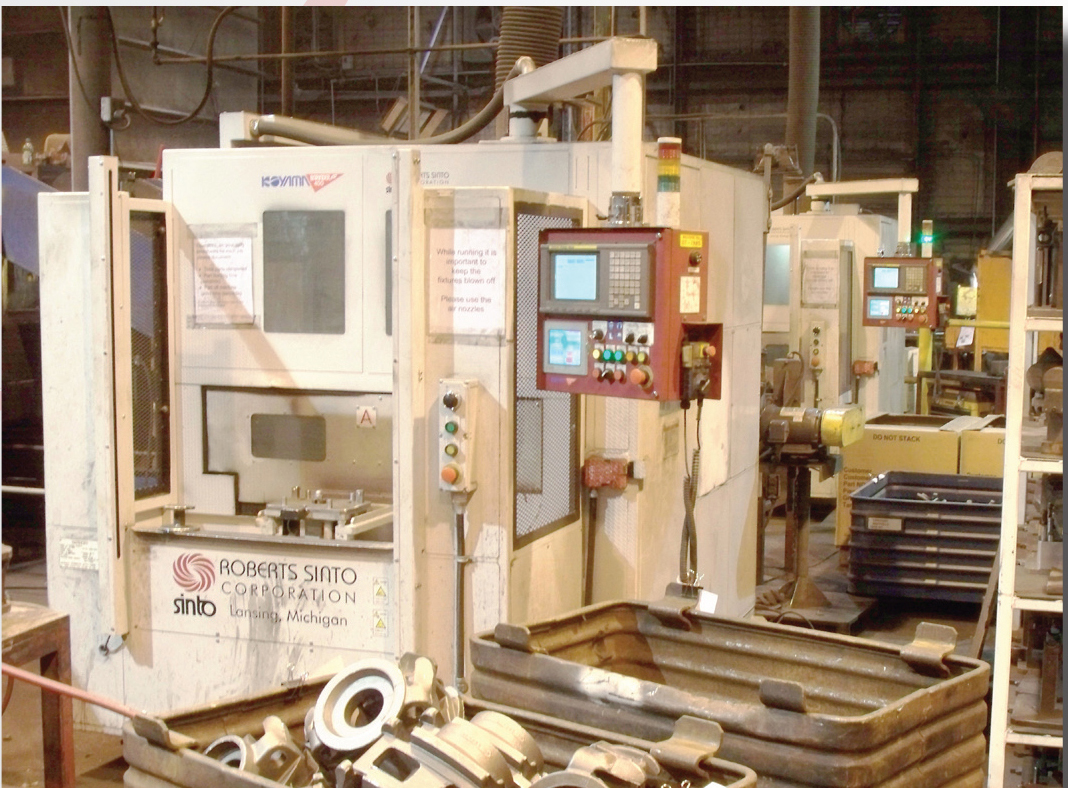
One operator is able to run both Barinders
Roberts Sinto Corp. has earned a reputation for providing solid, practical solutions to foundry operations and automated material handling problems. They are a world leader in the foundry industry, and are instrumental in connecting foundries with machinery that meets the highest standards of performance, productivity and quality. Their goals and demand for quality align perfectly with Farrar’s vision of being committed to being the preferred source of value and solutions.
“The BARINDER® is simply beyond comparison,” says Hicks. “This machine is robust. It’s healthy. It’s dependable for grinding repeatability. I just can’t say enough good things about these.”
By Allan Ross
Facts on the BARINDER® Grinder:
Features five axes of robotic part handling
Two machine styles: single station and turn table
Easy to learn, easy to program, easy to operate
One person can operate several machines
Can work in automatic mode with an operator or in tandem with robotic handling
The grinding wheels are designed to have a long life
Repeatable control-to-precision tolerances
Allows for fast product changeovers
Finishes complex interior surfaces
Designed for reliability and maintainability
Background of Roberts Sinto Corporation:
Roberts Sinto is a leader in the design and manufacture of foundry equipment, and complete foundry projects. Our equipment ranges from molding and core machines to complex handling systems. Our Flaskless Molding Machines have revolutionized the Flaskless molding market with over 100 in North America alone. With our experience, we are able to provide flaskless machines ranging from 14” x 19” to 32” x 32”. In addition, we have expanded our product line with the, Barinder grinder, the EconoPour automatic pouring system and surface treatment equipment (SST). Our experience and innovative global technology enables today’s foundry managers to meet the demands and expectations for quality castings and profitability in the 21st century.