Safe and Cost Effective Shot Blasting in the Aluminum Die-cast Industry
ABSTRACT:
In the die casting process, deburring and cleaning utilizing shot blasting equipment is often essential to enhance and/or improve the surface characteristics and quality of cast parts. Die casters use multiple types of abrasives for their blasting processes depending on a variety of factors.
This paper will introduce comparative data between cast shot and cut wire shot. This distinction is one of the most interesting to investigate due to the characteristics that differentiate these two families of abrasives. It is strongly recommend that customers use zinc abrasives to deburr and clean aluminum parts. This is primarily due to the lower explosion sensitivity of zinc abrasives and dust in comparison to other abrasives such as cast high or low carbon steel shot and cast or cut-wire stainless steel shot. Using zinc abrasives will minimize the risk of fire and explosion.
This paper will demonstrate the performance and safety differences between zinc and stainless steel cut-wire vs. cast products of the same materials.
INTRODUCTION:
In the author’s experience customers use various types of abrasives to clean and deburr aluminum castings. I have learned that different types of abrasives, meaning cast vs. cut-wire, act and perform differently in a given application. The cut-wire demonstrates improved value in two areas. Cleaning efficiency and in the rate of consumption.
Cleaning efficiency is perhaps most important of course because with a more efficient abrasive cycle times are shorter thus reducing the cost of the process both on an annual basis and from a marginal cost basis related to the cost per part. This is achieved by reducing the time required to complete a particular process. Less time affects the “total cost of ownership” in that it reduces all costs associated with the blasting process. Associated costs such as labor, energy, maintenance and wear parts and common costs such as freight and SG&A are all reduced with a more efficient abrasive media. Efficiently utilizing blasting equipment is always of benefit to the user and capacity increases are often not possible or impractical due to working capital requirements of the company.
Consumption of abrasive is important because it of course affects the cost of the abrasive and process but also from ecological and safety points of view. Lower consumption of abrasive results in less dust generation by the abrasive as it breaks down. Lower dust generation means lower disposal costs, less use of landfill to dispose of dust and lower risk of explosion in blast or dust collection equipment associated with the process.
DESIGN OF EXPERIMENTS (PROCEDURE OF DURABILITY TEST)
Using laboratory equipment in this case the Ervin Test Machine, it is possible to measure the kinetic energy of particles inside the test chamber by utilizing the “Almen test strip” holder located on the test machine. The almen strip is exposed to abrasive impacts by way of an opening in the test chamber that exposes the test strip to the abrasive inside the test chamber. The abrasive impacting the test strip will result in an arc being created as stress is imparted into the strip. The amount of curvature or arcing will determine the amount of energy transmitted into the strip. More or a higher degree of arc shows that more energy is being transmitted.
The second parameter tested was consumption. It is also possible to measure abrasive consumption by measuring the number of cycles a sample amount will last. By using 100g of abrasive sample, life of each abrasive can be evaluated. The procedure of the experiment is as following and it continues until 100g of sample is worn away. (See Fig.1)
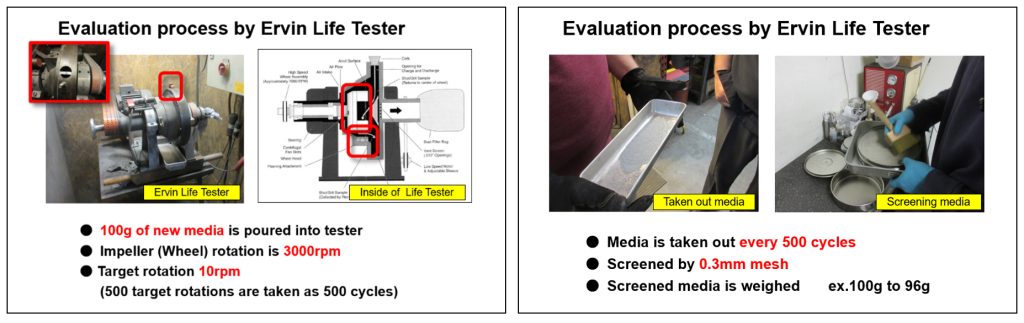
Fig.1 Procedure of durability test
EXPERIMENT #1 (LIFE TEST OF ZINC CAST SHOT VS ZINC CUT WIRE)
We tested CAST ZINC SHOT vs. ZINC CUT-WIRE media. Test results demonstrate the following. Cast zinc shot lasts 7,763 cycles whereas zinc cut wire shot lasts 11,165 cycles. It is also evident that the breakdown characteristics of the two products differ greatly. The number of broken media and very fine particles of cast zinc shot versus the more controlled breakdown and no broken zinc cut-wire shot particles as seen in the pictures taken after completion of the durability test. (See Fig.2)
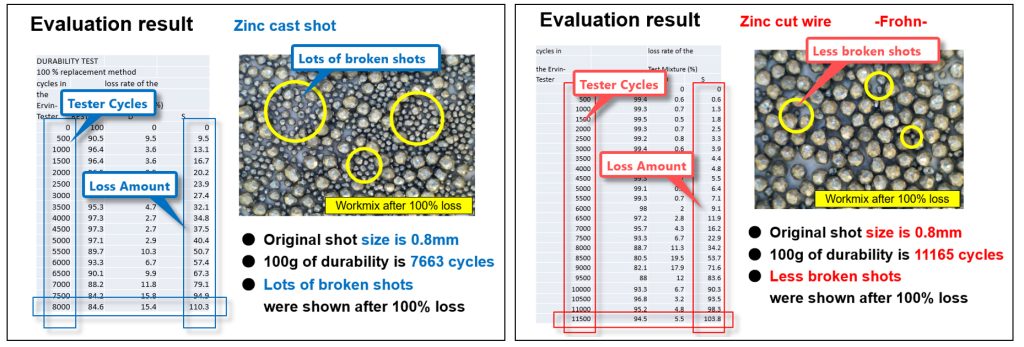
Fig.2 Result of durability test (zinc cast vs. zinc cut-wire)
EXPERIMENT #2 (LIFE & TRANSMITTED ENERGY TEST OF STEEL CAST SHOT VS. STEEL CUT WIRE SHOT)
Also tested were CAST STEEL and STEEL CUT-WIRE medias. It was possible to determine the amount of transmitted energy of these medias by utilizing the “Almen test strip” holder located on the Ervin Test Machine. The almen strip when exposed to impacts will arc as stress is imparted into the strip. The amount of curvature or arcing will determine the energy transmitted into the strip. More, or a higher degree of arc shows that more energy is being transmitted. In figure #3 below, it can be seen that the same sized particles of cut-wire media transmit 65% more energy than the cast steel shot. This demonstrates a higher degree of efficiency and cleaning ability and a potential to use this increased transmitted energy to shorten the time necessary to clean a part. (See Fig.3 and Fig.4). Also seen is the higher breakdown rate (consumption) of cast steel shot vs. steel cut-wire shot. The difference in consumption was shown to be 30% less with cut-wire shot.
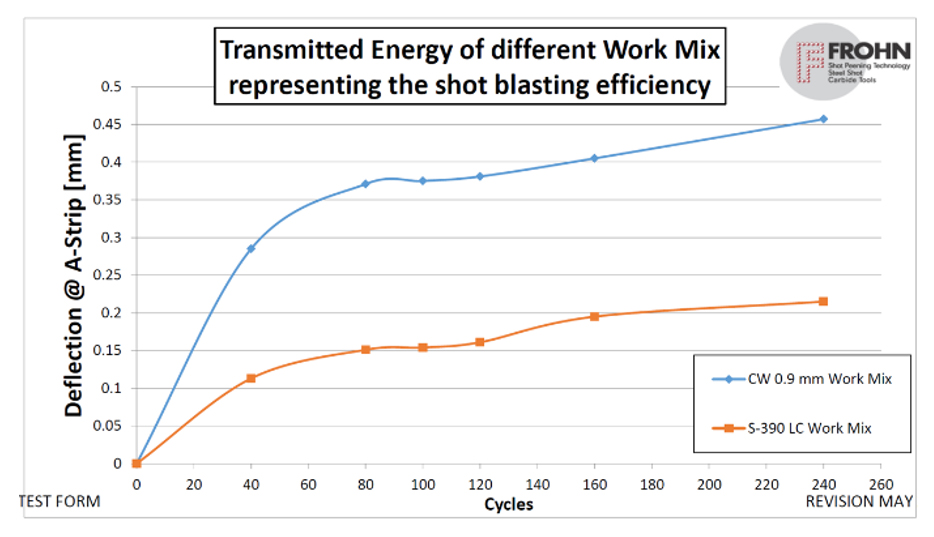
Fig.3 Comparison of transmitted energy

Fig.4 Comparison of durability
ACTUAL FIELD RESULTS AT our DRUM BLAST USER (STEEL CAST SHOT VS. STEEL CUT WIRE)
Based on the below performance data comparison the customer tracked in an actual field trial, the cut-wire shot provided overall savings to the blast process. The customer gathered baseline performance data using their original S-390 cast steel shot for a one week period. They then tracked the same metrics over a six week period and noted the changes using 0.9 mm cut-wire shot. After the 6 week trial, the results demonstrated that total operational costs of the blasting process were reduced by ~ 20% vs. cast steel shot. The marginal cost per part showed a reduction in cost of $.04 per piece or part. The higher particle density and improved microstructure of the cut-wire drove this cost reduction shown in the below results seen in (fig. #5).
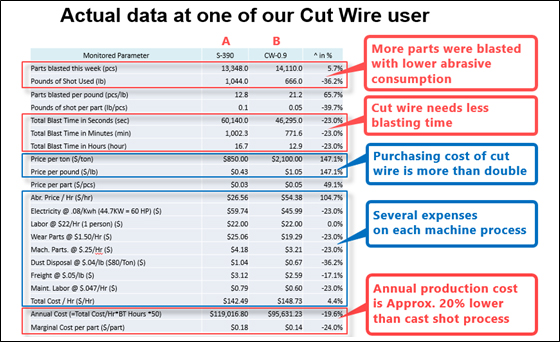
Fig.5 Field test result at drum blast user
CONCLUSION
Results of both laboratory testing and actual in-field trials show the advantages of cut wire abrasive media vs. cast abrasive media. We can conclude this advantage is not limited to the type of material itself, zinc, stainless steel, carbon steel or other metals. Laboratory experiment results of zinc cut wire will contribute cost reduction on operational costs of the blasting process. We can apply the field result to other customers in any industry. The advantages of cut wire products derive from an improved microstructure and density of each media particle.
The pictures below show new and operating mix media samples and the objectionable defects found. These pictures show that cast shot has more voids, cracks and elongations than cut wire shot when ground as per ASTM testing methods. (See Fig.6). This validates the claim of a superior product for use in surface finishing applications.
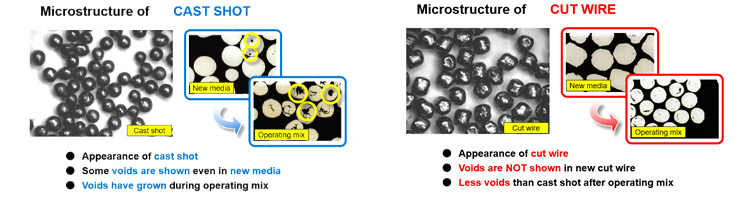
Fig.6 Difference of microstructure between cast shot and cut wire
Regarding as safety feature, the risk of dust fire and explosion greatly varies depending on the shot type. Based on the following comparison data we can say zinc is one of the safest material as abrasive product for shot blast process. (See Fig.7)
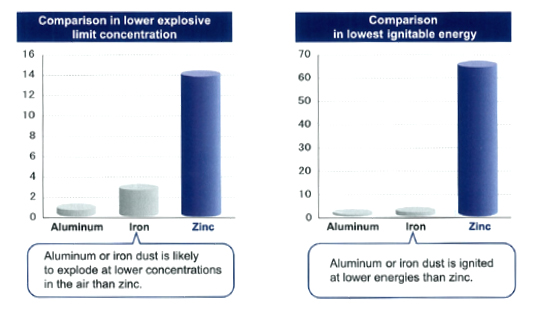
Fig.7 Comparison of lower explosive limit on each material
REFERENCES
All the figures 1-7 were researched by Sinto America.